ISOLATION AND CHARACTERIZATION OF CELLULOSE DERIVED FROM KOLA NUT ( COLA- STERCULIACEAE ) TESTA
Abstract
True cellulose in kola nut testa was isolated by the techniques of multi-stage pulping and bleaching using NaClO2 after initial delignification using NaOH as alkali. After identification by the iodated-ZnCl2 method, KT α-cellulose was evaluated for organoleptic properties and characterized according to physiochemical properties, inherent functional groups as well as surface morphology and degree of crystallinity. The results showed that 12.4% of granular, off-white, odourless, tasteless and insoluble KT α-cellulose was recovered from 150 g of extractive free KT. KT α-cellulose, characterized by a pH of 6. 4 and moisture sorption capacity of 1.8% as well as true, bulk and tap density values of 1.19, 0.29 and 0.43 gcm-3 respectively showed to contain 1.5% ash after carbonization. Fourier Transform Infra-red spectrophotometric (FTIR) analysis showed the presence of strong and broad absorption bands around 3257 cm-1 which were assigned to intermolecular and intramolecular stretching vibrations of the -O–H groups in KT α-cellulose. A sharp band identified near 2919 cm-1 was ascribed to the asymmetric and symmetric stretches of the –CH2 and –C-H bonds in the biopolymer. The scanning electron micrograph (SEM) of KT α-cellulose revealed that the biopolymer consists of irregularly shaped particles characterized by an average size of 33 ± 0.3 µm while the result of the X-ray diffraction analysis estimated the crystallinity index (CI) as 0.67 degree of crystallinity, thus, the proportion of crystallinity in KT α-cellulose and 35% of the particles as amorphous in structure. KT α-cellulose, therefore has great potential for use in the food, pharmaceutical and allied industries and is recommended as a way to promote creativity by turning wastes into wealth.
Keywords
Kola nut testa, cellulose, isolation, characterization, morphology, crystallinity α index, creativity
Introduction
The campaign for the use of natural fibre and other biodegradable polymers as a way to promote environmental sustainability and minimize pollution has stimulated the search for and recovery of cellulose from non-food sources, especially of plant origin. Moreover, the increasing global population has unrelentingly stretched the non-renewable petroleum sources from which virtually every synthetic item of use by man in medicine, engineering and construction derives, hence, the intensive research and evaluation of natural fibers as replacements for petrochemical based raw materials (Atiqah et al., 2019), if the global demand for consumable goods would not outstrip the supply in the nearest future. For example, (Ververis, 2007) found out that the global consumption of paper products which was about 300 MT in 1997 rose above 400 MT in 2010, occasioning the shortage of pulping raw materials and increased the demand for paper products. As uncontrolled deforestation inevitably challenges the sourcing and availability of natural raw materials, such as wood fibre for cellulose production, new and alternative raw materials sources are being explored for across the globe (Khenblouche, 2019) ; (Bolio-López, 2015) . Consequently, non-wood sources, especially among agricultural wastes are currently being investigated for their prospects as raw materials for cellulose production (Yusrina, 2018); (Ashraf, 2016) ; (Chaudhary, 2012) and (Ververis, 2007).
Cellulose (poly(1,4-β-D-glucopyranoside) C6H12O6), the chief constituent of plant cell walls is the most abundant organic matter found in nature (Bennehalli, 2019); (Figen, 2016) ; (Rojas & Azevedo, 2011), accounting for about half to one-third of all plant tissues (Khenblouche, 2019) ; (Penjumrasa, 2014) and over 50% of all the carbon found in the vegetable kingdom (http://chem.libretexts.org/link?166792) and used widely in various manufacturing industries as well as petroleum and mineral processing (Abe, 2018); (Macuja, 2015); (Saelee, 2014). An isomer of starch, it is a high and linear polymer, the building block (molecular chains) of which is an anhydride of glucose linked through a covalent bond (β-glycosidic bonds) at the C1 oxygen to glucose of a ring and the adjacent ring C4 (4th position) (Bennehalli, 2019) (Bennehalli et al., 2019; (Bolio-López, 2015) (shown in Figure 1) to produce a structure that is more extended than amylose.
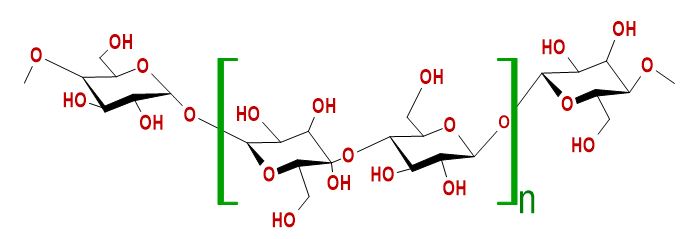
The excellent linearity allows large interaction by hydrogen bonding between OH groups on adjacent chains, enabling close packing into fibres (high crystallinity) with the effect that cellulose does not dissolve in water (Bennehalli, 2019); (Nazir, 2013) or any other solvent. Yielding D-glucose as the end product of acid hydrolysis, man, like other vertebrates cannot breakdown this vast component of essential and fibre-rich vegetable sources in his diet to the much-desired energy-giving glucose due to lack of β-glycosidic bond (β-acetal linkage) hydrolyzing enzymes in his gut (http://chem.libretexts.org/@go/page/30355). As a result, there is growing demand for cellulose fibres of vegetable origin (Bolio-López, 2015), especially, from non-food sources since they are photosynthetically regenerated (Khenblouche, 2019); (Draman, 2016) (Draman, 2016) ; (Penjumrasa, 2014); (Nazir, 2013) and their utilization for industry processes is unlikely to negate the global campaign against hunger.
Cellulose is useful to man and has been exploited in many areas, including: wood for building; pulp for paper making; cotton, linen and rayon for clothing and textiles; cellulose compounds such as nitrocellulose/cellulose nitrate (NC) for explosives, lacquer and other wood finishes as well as cellulose acetate, including cellulose acetate resin and sheet, cellulose triacetate, cellulose propionate, cellulose acetate propionate (CAP) and films, cellulose acetate butyrate (CAB), micro crystalline cellulose (MCC), carboxymethyl cellulose (CMC), sodium CMC (Na-CMC), potassium cellulose succinate, cellulose acetate trimellitate etc., waste management and environmental protection; design of absorbents for oil spill and heavy metals pollutants in water or on land and for making filters for industrial and municipal wastewater treatment), cosmetics, adhesives as well as in food and pharmaceutical preparations, necessitating its recovery from the numerous and abundant agricultural wastes which need disposal (Khenblouche, 2019); (Bennehalli, 2019); (Abe, 2018) ; (Figen, 2016) ; (Penjumrasa, 2014); (Saelee, 2014); (Rojas et al., 2011) .
The processing of kola nut seeds of the economically important fruit of the kola tree for masticatory and social functions as well as utilization in the food and pharmaceuticals industries (Akinnagbe & Ikusika, 2016) (Akinnagbe and Ikusika, 2016; (Atanda, 2011); (Burdock, Carabin, & Crincoli, 2009) Burdock et al., 2009 results in the generation of huge volumes of kola nut testa or skin as waste from the over 300,000 tons annual global kola nut production (Fabunmi, 2019) ; (Asogwa, 2012) ; (Asogwa, 2012) (Hamzat, Omole, Babatunde, Adejumo, & Longe, 2007) Despite the reported presence of rich fibre and polyphenol matter in this waste, it is haphazardly thrown to deface the environments, rot and cause pollution problems (Agboeze, Uchechukwu, & Ogbobe, 2020) ; (Lowor & Ofori, 2018). While (Žmak, 2014) acknowledged the burden of waste disposal on our society, (Fritsch, 2017) campaigned for processing strategies and value-added exploitation of the enormous and beleaguering agricultural wastes, including kola nut testa in order to circumvent the imminent natural disaster of converting wealth into wastes (Pappu, 2011). Having found and reported the extraction of cellulose from Areca husks as an alternative and safe method to manage the overbearing Areca wastes (Bennehalli, 2019), (Bukola, 2018)listed beneficial kola nut wastes derivative products and certified its transformation as a gallant approach to mitigate the challenging environmental pollution associated with agricultural wastes. Kola nut testa can be harnessed, the polyphenols recovered and exploited as a cellulose source for industry operations while serving the tripartite role of boosting farmers’ economy, environmental clean-up and guaranteeing that the poorest nations likewise benefit from waste management technologies (Achor, 2014); (Chaudhary, 2012) ; (Ohwoavworhua, 2005) ; (Kathiravale, 2008) .
Occurring seldomly in the free state, cellulose, known variously as pure cellulose or alpha cellulose (Macuja, 2015) , α-cellulose, true cellulose or resistant cellulose is generally associated with other substances like lignin (phenolic polymeric compounds), varying amounts of other polyssacharides such as hexosans, pentosans, glucosan, polyuronides (collectively known as hemicellulose and comprising of branched and lower molecular weight β-cellulose and γ-cellulose), fats as well as waxes, resins, traces of minerals and colouring matters (Bennehalli, 2019) ; (Nazir, 2013).. α-cellulose is stable and resistant to the effect of 17.5% NaOH at RT but β and γ-celluloses are not stable to the action of 17.5% NaOH. (Nwachukwu & Ugoeze, 2018); (Abe, 2018) ; (Yusrina, 2018) ; (Abe, 2018); (Hisan & Amin, 2017); (Macuja, 2015) ; (Saelee, 2014); (Pachuau, 2014) ; (Azubuike & Okhamafe, 2012) ; (Ohwoavworhua, 2005); (Ververis, 2007); (Ohwoavworhua, Adelakun, & Okhamafe, 2009); (Samia, 2016) and several others have used various techniques and processing conditions to isolate and estimate α-cellulose from a variety of agricultural wastes substrates, including Luffa cylindrica, rice and groundnut husks, cotton stalk pulps, hosiery waste, corncobs, Sorghum caudatum, water hyacinth, bamboo (Dendrocalamus asper); algal biomass and citrus peels; sugarcane bagasse; orange mesocarp; sawdust; Buchanania cochinchinensis and Saccharum officinarum which have been utilized in various industry processes to produce a variety of products as well as converted into numerous other useful products (Alabi et al., 2020); (Onigbinde & Adeago, 2015); (Supranto, Tawfiequrrahman, & Yunanto, 2014); (Hossain, 2015); (Hossain, 2015); (Kopania, Wietecha, & Ciechańska, 2012); (Rojas et al., 2011); (Israel, 2008). The methods, unique in the advantages of producing cellulose of varying purity have limitations and essentially involve the removal of lignin, leaving the hollocellulose mixture of cellulose and hemicelluloses, the latter which is separated by extraction and solubilization after hydrolysis of the mixture using an aqueous alkali. The aim of the present study is to isolate α-cellulose in kola nut testa. Lignin would be removed from kola nut testa after extracting the soluble matter before separating the kola nut testa α-cellulose from the hemicelluloses. The α-cellulose isolated from kola nut testa would be characterized according to standard properties and areas of utilization suggested.
Materials and Methods
Materials
In addition to kola nut testa which was collected from Ogbete market, Enugu, Nigeria, the following reagents: NaOH, HCl, HNO3, C2H5OH (EtOH), ZnCl2, NaNO2, KI, toluene, NaClO2, ether, double distilled water (DD H2O) and others used in the study were of analytical grade, purchased from Bristol Scientific Nigeria, Lagos and were used without further purification.
Equipment List
Fourier Transform Infra-red (FTIR) Spectrophotometer [Buck 530IR] range: 4550-650 cm-1, manufactured in England, Phenom Prox scanning electron microscope (SEM) S/No: Q15ORES manufactured by Phenom World Eindhoven, Netherlands, Phillips PW 1710 X-ray diffractometer (XRD) manufactured by Philips X-ray Analytical, Amsterdam, The Netherlands, Jenway 3510 pH meter, USA, Barnstead electrothermal heating mantle UM0500BX1, Wolflabs LTE Scientific OP100-U digital oven; 100l volume as well as Stampfvolumeter (Model STAV 2003 JEF, Germany) and 250°C maximum temperature BAT7149-Clifton shaking water bath NE5 28 were used in the study.
Methods
Sample Preparation and Pre-treatment
Having manually sorted to remove foreign matter, kola nut testa was washed to remove adhering dust and air-dried for 2 days after which it was dried in the oven for 24 hrs at 60°C. It was subsequently milled to obtain 250 μm particle size and allowed to cool down before transferring to a clean and dry polyethylene bag. Processed kola nut testa, labelled KT was stored in the laboratory until it was subjected to extraction by means of a soxhlet and following a modified method of TAPPI 1997 in which 2:1 v/v toluene-ethanol mixture was the extraction solvent. The pre-treated/defatted/extractive-free KT was dried at room temperature (RT) before using for the pulping procedures.
Isolation of α-Cellulose
NaOH Pulping
Extractive free KT was first delignified by digesting a 150 g sample in a stainless steel container with 2 L of 2 % w/v NaOH for 4 hrs according to a revised method of Nwachukwu and Ugoeze (2018). The container had been immersed in a water bath at 80 oC. At the end of the process, excess NaOH was decanted from the saturated mass of sample and the latter liberally washed with DD H2O until it tested neutral to red litmus paper. The resulting cake was transferred to a piece of clean white muslin cloth and excess H2O squeezed from it.
Multi-stage Pulping/ Bleaching
The procedure reported by Ohwoavworhua et al. (2009) was adopted for the multi-stage pulping
but with some adjustments. For this purpose, 150 g of delignified and extractive-free KT (2.1.3a) was added to 2 L of 3.5% HNO3 containing 20 g of NaNO2 in a stainless-steel container. The latter was immersed in a water bath and the mixture digested for 2 hrs at 90°C in order to solubilize the lignin and remove it as nitrolignin. At the end, the mixture was thoroughly washed with DD H2O and filtered before bleaching using a modified procedure developed from combining the methods of Yusrina and Sutriyo (2018) and Ohwoavworhua et al. (2009). After adding 400 mL of a 1: 1 aqueous mixture of 3.5% NaClO2 to the residue in a 1 L beaker, it was heated to boil for 10 mins at the end of which it was liberally washed with DD H2O, and filtered to obtain KT holocellulose. The later was further delignified by transferring to a 2 L Erlenmeyer flask holding 1 L of 17.5% w/v NaOH and heating for 1 hr at 80 oC. Thereafter, the mixture was filtered and liberally washed with DD H2O until the filtrate tested neutral to red litmus paper. The resulting α-cellulose was further whitened and the extraction process completed by bleaching for a second time by treating with 200 mL of 1:1 aqueous mixture of 3.5% NaClO2 for 5 mins at 100 oC. KT α-cellulose was washed and filtered until the filtrate became clear, excess water manually squeezed out and then dried as small lumps in an oven for 2 hrs at 60 oC. It was finally weighed and the yield calculated from the formula:
Where:
W2 = weight of the α-cellulose residue
W1 = weight of the holocellulose sample.
Characterization
Following identification by the action of iodated-ZnCl2, KT α-cellulose was tested for the organoleptic properties of appearance, colour, taste and smell and characterized according to the physiochemical properties of ash content, solubility in common laboratory solvents (dilute acid and base, ethanol and ether), pH as well as density (true density, bulk density and tap density) and moisture absorption. Fourier Transform Infrared Spectrometry was used to determine the functional groups present while the surface structure (morphology) and degree of crystallinity respectively were determined by means of a scanning electron microscope (SEM) and X-ray diffractometer (XRD).
Identification of α-cellulose in KT
KT α-cellulose was identified by following the standard method for the identification of powder cellulose. Exactly, 10 g of the free-flowing KT α-cellulose powder was dispersed from a watch glass into 2 mL of a solution prepared by dissolving 20 g of ZnCl2, 6.5 g of KI and 0.5 g of I2 crystals in 10.5 mL of DD H2O and shaking for 15 mins.
Organoleptic
The organoleptic properties of α-cellulose derived from KT was estimated by the method described by Yusrina and Sutriyo (2018). Precisely, the appearance, colour as well as taste and smell of KT- α-cellulose were appraised after placing a portion of the free-flowing powder on a white base.
Determination of Ash
Ash in KT α-cellulose was determined by the method of Rowell et al. (2012). Having cleaned and ignited two empty 50 mL marked porcelain crucibles and their covers to constant weight in a muffle furnace at 575 oC, they were removed, left to cool slightly and desiccated. Both crucible and cover were promptly weighed to the nearest 0.1 mg after which approximately 5.0 g of sample was placed in each of the crucibles. Using a pair of thongs, the crucibles and the contents were placed in the muffle furnace at the same temperature and the covers leaned beside them before closing the door of the furnace. After 3 hrs, when the sample had ignited and the samples turned to ash, the crucibles were removed from the furnace and the covers replaced while letting to cool slightly on the bench. They were later placed in the desiccator, allowed to cool down and weighed to the nearest 0.1 mg. The ash content was reported as the average of two results obtained from a calculation that expressed the ash as a percentage of the sample using the formula below.
Where:
A= weight of ash, g
B= weight of KT α-cellulose test specimen (g)
Solubility Test
The solubility of KT α-cellulose in H2O, ethanol, ether as well as dilute NaOH and HCl was determined by discharging a little quantity of the powdered sample held in a spatula into a 50 mL beaker containing 10 mL of the particular solvent. Interface between the sample and the solvent was facilitated by stirring the mixture using a flat end glass rod after which the mixture was left to stand for 5 mins and thereafter examined for solubility.
pH Determination
The method described by Ohwoavworhua and Adelakun (2005b) was used to determine the pH of KT α-cellulose. After adding 2 g of the powder to 100 mL of DD H2O in a 250 mL beaker, the mixture was shaken for 5 mins after which the beaker was rested on the bench. When the precipitate had settled, the pH of the supernatant was tested using the pH meter.
Determination of True Density
The liquid displacement method using xylene (Sg 0.86) as the immersion fluid described by Ejikeme (2008) and Ohwoavworhua and Adelakun (2005b) was adopted for the determination of the true density of KT α-cellulose but with little variations Having weighed and recorded the weight of a clean and dry empty 50 mL pycnometer, the pycnometer was filled with xylene, capped and excess fluid dabbed from it using Kimberly laboratory wipes. It was reweighed before reducing the liquid in it by about 50%. Subsequently, 1 g of KT α-cellulose powder was fed into the pycnometer using a 30 x 56 x 30 x 4 mm borosilicate glass powder funnel. Xylene was supplemented to fill the pycnometer after which the later was capped and wiped dry of excess fluid. Its weight was again determined and the true density (Dt) calculated from the average of triplicate determinations using the formula:
Dt = W/[(a + W)- b] x Sg (3)
Where w is the weight of KT α-cellulose powder, Sg is specific gravity of xylene, a is the weight of the bottle + xylene and b is the weight of the bottle + xylene + KT α-cellulose powder.
Determination of Bulk Density
The bulk density of the α-cellulose recovered from KT was determined by the method described by Nwachukwu and Ugoeze (2018). 20 g of sample powder was poured into a clean and dry 100 mL Thermo Scientific Nalgene plastic measuring cylinder standing on a horizontal laboratory bench. After smoothing with a flat-end spatula, the volume occupied by the sample was determined and recorded as the bulk volume (Vb). The bulk density (Db) was later calculated from the model:
Bulk density (Db) = W/Vb (4)
Where W is the weight of the KT α-cellulose powder and Vb, the bulk volume.
Determination of Tapped Density
Using the same set up for the determination of Db, the tap density (Dtp) of KT α-cellulose was estimated by the method described by Ohwoavworhua et al. (2009). KT α-cellulose tapped volume was measured by determining the volume occupied by the sample powder after 500 taps by a Stampvolumeter. The tap density (Dtp) was then calculated from the equation:
(Dtp) = W/V500 (5)
Where W is the weight of KT α-cellulose powder and V500 is the tapped volume.
Moisture Sorption Capacity
The method of Achor et al. (2014) was used for the determination of the moisture sorption capacity of the α-cellulose extracted from KT. After evenly distributing 1 g of sample powder in a 70 mm petri dish of predetermined weight, the dish was placed on the plate of a 250 X 330 cm DWK Life Sciences KimbleTM desiccator equipped with a plastic knob and holding a full reservoir of DD H2O (RH = 100%). The set up was left to stand for 5 days at RT at the end of which the weight gain by the exposed sample was determined and recorded. The amount of moisture absorbed by the sample was then calculated as follows:
W2-W1/W1 x 100 (6)
Where, W1 and W2, respectively are the weights of the sample before and after exposure to moisture.
Fourier Transform Infrared (FT-IR Spectroscopy
The chemical groups present in KT α-cellulose were determined on the FT-IR spectrophotometer by homogenously mixing 1 mg of sample powder with 99 mg of KBr and pelletizing same by compressing in the disc. IR measurements were carried out in the range of 4550 and 650 cm-1 with a resolution of 8 cm-1. Analysis was conducted in duplicate and the differences in the results were insignificant.
Scanning Electron Microscopy (SEM
The method described by Benavent-Gil and Rosell (2017) was adopted to investigate the surface characteristics of KT α-cellulose using the Phenon Prox instrument, Phenon world Eindhoven, Netherlands scanning electron microscope (SEM). The sample was gold-coated with the aid of Quorum Q150R ES sputter coater operating on a sputter current of 20 mA and at 60 secs sputter time. After mounting the sample on the sample holder, micrographs (SEM) were recorded of images taken at an accelerating voltage of 15 Kv and a magnification of 500 x. Microstructure and image analysis was carried out by analyzing several points on the micrograph to determine the average particle size on a scale of 3cm: 100 μm.
X-ray Diffraction (XRD Analysis)
The degree of crystallinity of the α-cellulose isolated from KT was determined using a Phillips PW 1710 X-ray diffractometer (XRD) manufactured by Philips X-ray Analytical, Amsterdam, The Netherlands. The diffractometer, equipped with a monochromatic Cu-Kα X-ray generator (radiation lamp) operating at 40 kv and 30 mA and supplying radiation of wavelength (λ); 1.540 Å was set at wide angle goniometer. The sample had been prepared by pressing 2g of KT α-cellulose sample powder into the cavity of the sample holder and flattening with a glass slide before mounting on the instrument. The diffraction pattern was recorded over a temperature range of 5-90oC at a scan step rate of 0.2oC /sec and 2θ. At the end, the diffraction pattern was matched with the Powder Diffraction File Database to determine the average size of the sample crystals and the crystallinity index (CI), calculated using the expression of the peak intensity method described by Galiwango et al. (2019):
(7)
Where I200 is the maximum intensity of the principal peak (at about 2θ = 22) lattice diffraction and Iam, the minimum intensity of the diffraction corresponding to the amorphous phase at about 2θ =18.
Results and Discussion
The result of the determinations of moisture in KT, yield as well as organoleptic and the physiochemical characteristics of the α-cellulose isolated from KT are tabulated in Table 1. The FT-IR spectra, SEM and the diffractogram of the same are shown in Figures 2, 3 and 4 respectively.
Test |
Result |
Yield |
12.4% |
pH |
6.4 |
Organoleptic properties |
Odorless, off-white, tasteless granular powder |
Identification |
Turns violet blue with iodinated ZnCl2 |
Solubility |
Insoluble in H2O, ethanol, ether, dilute NaOH and HCl |
Ash content |
1.5% |
True density Bulk density Tap density |
1.19 gcm-1 0.29 gcm-1 0.43 gcm-1 |
Moisture sorption capacity |
1.8% |
Yield and Physicochemical Characteristics
Yield
Although the 12.4% yield of α-cellulose from KT was low in comparison with the amounts of the same biopolymer reportedly recovered from other agrowastes such as oil palm empty fruit bunches (64%); orange mesocarp (62.5%); durian rind (33.1%); raw cotton of cochlospermum planchonii (32%); maize cob (30%); lageriana siceraria (water gourd) fruit (29%); petioles of Tó (calathea lutea) leaves (26.3%) and betung bamboo (dendrocalamus asper) (28.6%) respectively by Nazir et al., (2013); Ejikeme, (2008); Penjumrasa et al. (2014); Ohwoavworhua and Adelakun (2005a); Okhamafe and Azubuike (1994) as well as Achor et al. (2014); Bolio-López et al. (2015) and Yusrina and Sutriyo (2018) in the eco-friendly extraction and characterization of cellulose from oil palm empty fruit bunches; investigation of the physicochemical properties of MCC from agricultural wastes I: orange mesocarp; extraction and characterization of cellulose from durian rind; some physical characteristics of MCC obtained from raw cotton of cochlospermum planchonii; direct compression studies on low-cost cellulose derived from maize cob and the extraction and characterization of MCC obtained from the back of the fruit of lageriana siceraria (water gourd) as well as the extraction of cellulose fibers from Tó leaf petioles (calathea lutea) and the characterization and preparation and characterization of MCC produced from Betung bamboo (dendrocalamus asper) through acid hydrolysis, it compared significantly well with the 14% yield of α-cellulose derived from corn cob (AC-CC) by Ohwoavworhua and Adelakun, (2005b) in phosphoric acid-mediated depolymerization and decrystallization of α-cellulose obtained from corn cob: preparation of low crystallinity cellulose and some physicochemical properties and outsized the meagre 4.8% yield of α-cellulose reportedly recovered from groundnut husk by Ohwoavworhua et al. (2009) after stretching the succeeding bleaching cycle from 5 to 10 mins in processing pharmaceutical grade MCC from groundnut husk: extraction methods and characterization. With the advocacy by governments across the globe for self-reliance, job creation and the clarion call to keep wastes off the streets, gathering of kola nut testa from processing points and the utilization of the α-cellulose recovered from it for various uses would stimulate large scale kola nut cultivation, reduce the cost of producing KT α-cellulose and ultimately justify the economics of this venture and the associated technological breakthrough with a capacity to establish Nigeria, its sister West African countries of Gabon, Ghana and Ivory Coast as well as Brazil and the West Indian Islands (Agboeze et al., 2020) as economic giants.
Ash
KT α-cellulose was found to contain an average of 1.5% ash. Achor et al. (2014) explained the 2.5% ash reported for epicarp of Lageriana siceraria (water gourd) fruit as an indication of the inorganic matter content of the biomass and corroborated Ohwoavworhua et al. (2009) and Ohwoavworhua and Adelakun (2005b)’s declaration about the significance of the ash gathered after burning a substance as a pointer to the overall precautionary measures undertaken during its processing. Ohwoavworhua et al. (2009)’s very low 0.38% ash obtained from groundnut husk was credited to the negligible presence of inorganic compounds generally acknowledged for cellulosic materials. The 1.5% ash realized from KT α-cellulose in this study lie between the 0.12% and 2.4% values reported for the same substance by Ohwoavworhua and Adelakun (2005a) and Ohwoavworhua and Adelakun (2005b) respectively from raw cotton and corn cob in some physical characteristics of MCC obtained from raw cotton of cochlospermum planchonii and phosphoric acid-mediated depolymerization and decrystallization of α-cellulose obtained from corn cob: preparation of low crystallinity cellulose and some physicochemical properties which both researchers as well as Yusrina and Sutriyo (2018) acknowledged meet the specifications of the British Pharmacopoeia 2004.
pH of KT
The observed 6.4 pH of KT α-cellulose was reported by Ohwoavworhua et al. (2009) to meet the requirement of the British Pharmacoepiea, which is a legally binding collection of standards and quality specifications for medicines and pharmaceutical raw materials, excipients as well as intermediates and finished pharmaceutical products used in Britain and the countries of the commonwealth (The International Pharmacopoeia, 2013).
Density
Bulk density gives an estimate of the ability of a powder material to flow from a height into the opening of a device intended to receive it for processing while tap density is a measure of how well a powder can pack in a confined space with repeated tapping (Azubuike and Okhamafe, 2012). Flowability and flexibility by rearranging under compression were clarified by the duo as pointers to a material’s high bulk and tapped densities. The values for both properties of the α-cellulose recovered from KT was corroborated by (Yusrina, 2018) to suggest that KT α-cellulose has excellent flow properties and therefore, suitable in applications requiring the use of fine flowing cellulose, such as the preparation of certain foods, pharmaceuticals and body cosmetics. True density, on the other hand which defines the precise density of a solid material, exclusive of volume contributions from system pores has been purported to equate the theoretical density of the material at some spatial and symmetrical arrangements assumed by the atoms, constituting material’s building blocks; hence, its description as a gateway to elucidate the packing arrangement of a material’s building block (Achor et al. (2014). True, bulk and tap density values for KT α-cellulose respectively which are 1.19, 0.29 and 0.43 gcm-3 lie between 1.60, 0.35 and 0.42 and 1.76, 0.424 and 0.596 gcm-3 reported by Azubuike and Okhamafe (2012) and Ejikeme (2008) for corn cobs MCC and orange mesocarp MCC in the physicochemical, spectroscopic and thermal properties of MCC derived from corn cobs and the investigation of the physicochemical properties of MCC from agricultural wastes I: orange mesocarp.
Moisture Sorption Capacity
Moisture sorption capacity of a substance is a measure of the sensitivity of the material to moisture, dampness, humidity, wetness or vapour. The determination of water sorption property of a material is significant because it enables a perception of the physical stability of secondary items, such as medicinal tablets, paper wipes etc. derived from the material when such items are stored in humid environments. The moisture sorption capacity of KT α-cellulose in this research, found to be 1.8% and significantly lower than the 4.12% and 4.47% reported by (Yusrina, 2018) and (Ohwoavworhua, 2005b) respectively for betung bamboo (dendrocalamus asper) and corn cob suggests that medicinal tablets produced from α-cellulose extracted from KT would demonstrate higher stability and less sensitivity to damage by atmospheric moisture than that supposedly prepared from the groundnut husk α-cellulose, explored by Ohwoavworhua et al. (2009). Highlighting the remark by Ohwoavworhua et al. (2009) that cellulose of significant crystallinity demonstrates low moisture absorption capacity proportional to the amount of the complement amorphous cellulose, Ohwoavworhua and Adelakun (2005b) corroboratively implied that the molecular structure of the particles of the α-cellulose isolated from KT is crystalline rather than amorphous. It therefore infers that KT α-cellulose can be utilized in applications where celluloses of poor moisture sorption properties are unsuitable. This, ultimately would lead to savings from additional cost that ordinarily would have been incurred to provide for moisture trap or retardant in a secondary item.
Organoleptic
The Organoleptic properties of the α-cellulose isolated from KT: off-white in colour, odourless, tasteless and granular to feel (texture) had earlier been reported by Achor et al. (2014) and Okhamafe and Azubuike (1994) as satisfactory and desirable.
FTIR
Figure 2 shows the Fourier Transform Infra-Red Spectra of the α-cellulose recovered from KT.
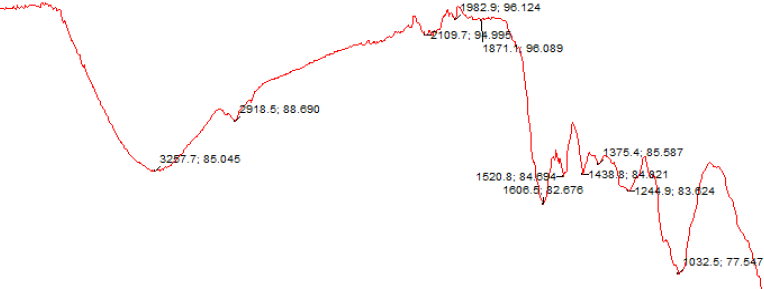
Comparison of the characteristics bands in the spectra with those earlier reported for the FTIR spectra of α-cellulose derived from various other plant sources showed several similarities (Galiwango, 2019) ; (Gonultas, 2018) ; (Ivanova, Korolenko, & Korolik, 1998) ; (Poletto, Júnior, & Zattera, 2014) including the strong and broad band in the neighbourhood of 3257 cm-1 which was assigned to different -O–H (intermolecular and intramolecular) stretching vibration modes and another relatively sharp band around 2919 cm-1 ascribed to the asymmetric and symmetric stretches of the –CH2 and –C-H bonds in KT α-cellulose. The various absorption bands found in the fingerprint region of the spectra are explained thus. Intermolecular hydrogen bonding between adjacent α-celluloses in KT, contributions from in-plane -O-H bending vibrations and -CH2 deformation respectively are suggested to be responsible for the absorption bands at 1438 and 1375cm-1. The dual bands at 1520 cm-1 and 1506 cm-1 which are due to stretching vibrations of -C=C- in a ring system are thought to emanate from KT lignin which might have retained, thus contaminated the product. Gonultas and Candan (2018) associated the absorptions bands around 1515-1506 cm-1 to the -C=C- stretching of the aromatic constituents of the lignin present in the aromatic-rich wood in the chemical characterization and FTIR spectroscopy of thermally compressed eucalyptus wood panels. Poletto et al. (2014) reported IR absorption bands at 1460, 1425, 1335, 1220 and 1110 cm−1 which were ascribed to bending and stretching vibrations as well deformations of the -C–H, -C–O- bonds/groups in the lignin and polysaccharide units of the different wood flour samples in native cellulose: structure, characterization and thermal properties. The absorption band at 1244 cm-1 is ascribed to stretch movements of the -C-C- and -C-O- bonds while the strong peak at 1032 cm-1 is credited to the stretching vibration of the -C–O–C- bond in the pyranose rings (β-1-4- glycosidic linkages) of KT α-cellulose as previously reported by (Sun, 2004) in the comparative study of crude and purified cellulose from wheat straw.
SEM of KT α-cellulose
The SEM showing the surface characteristics of the α-cellulose in KT is presented in Figure 3.
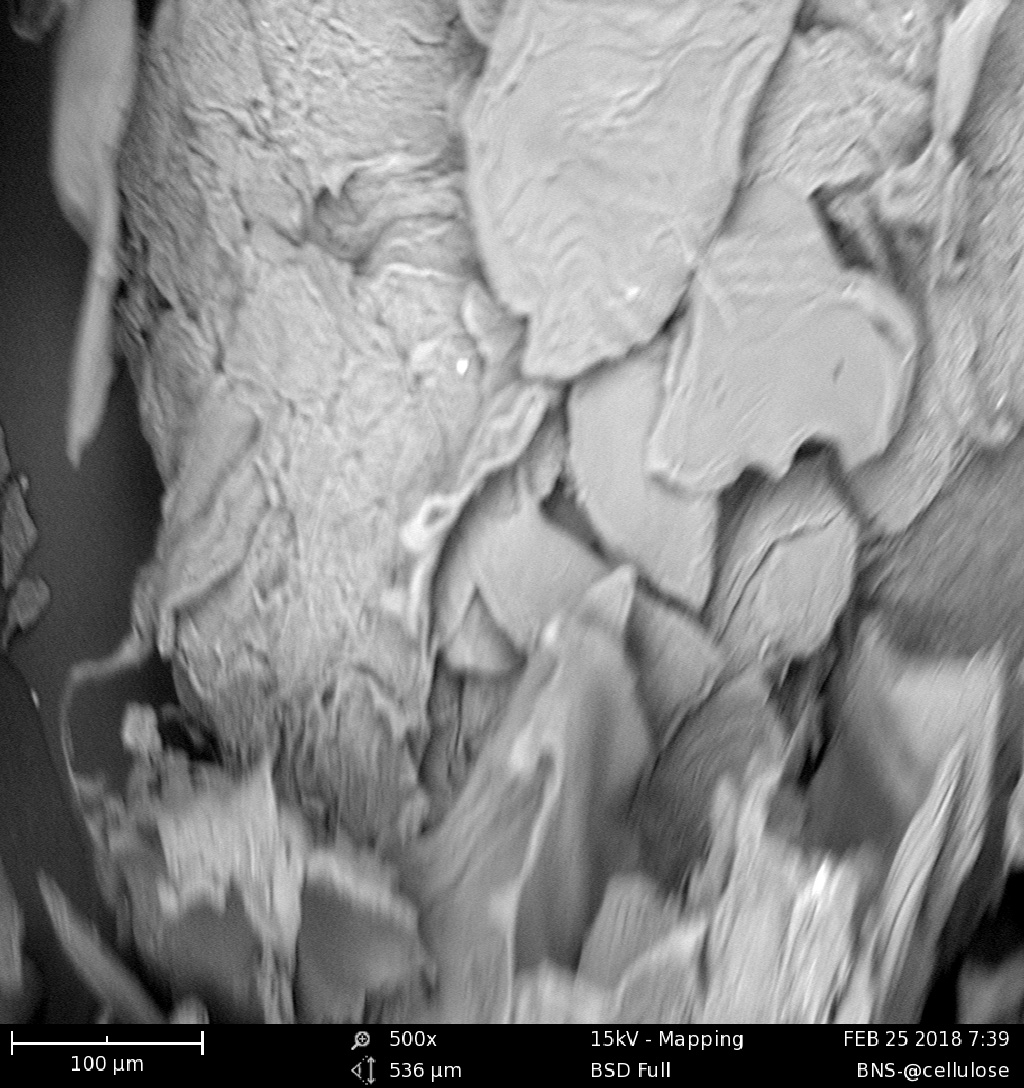
The micrograph shows that KT α-cellulose consist of irregularly shaped particles characterized by an average size of 33 ± 0.3 µm. While α-celluloses derived from different parts of the date palm tree by (Galiwango, 2019) in the isolation and characterization of cellulose and α-cellulose from date palm biomass waste were reportedly described as a twisted distribution of particles characterized by non-uniform macrofibril shapes, the morphologies of the cellulose particles isolated from waste pulps of carrot, cucumber, apple and tomato by Szyman´ska- (Chargot, 2017) in the isolation and characterization of cellulose from different fruit and vegetable pomaces showed uniform distributions of cellulose microfibrils of correlated thicknesses. The micrograph of the durian rind cellulose studied by (Penjumrasa, 2014) in the extraction and characterization of cellulose from durian rind reportedly showed a scattering of the non-fibrous components over the surface of the biomass. The cellulose microfibers isolated from Retama raetam stems by Khenblouche et al. (2019) in the extraction and characterization of cellulose microfibers from Retama raetam stems which were found to be smaller than those produced from sisal and agave fibre as well as coconut palm leaf, soy hull and wheat straw sources were projected to be beneficial as reinforcing agents in biodegradable composites as well as gel formation and additives in cosmetics and foods respectively.
XR-D of KT α-cellulose
The diffractogram of the α-cellulose isolated from KT is presented in Figure 4.
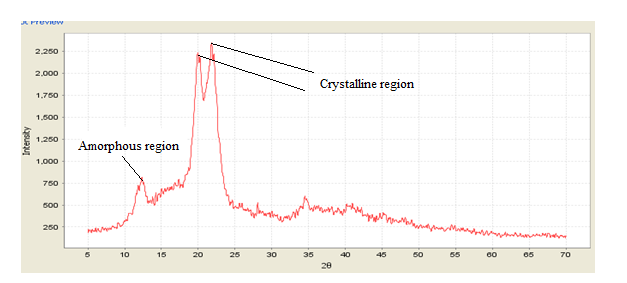
From expression (7), I002 was captured around 2400 while Iam showed around 800. Substituting these in the equation of the peak intensity therefore gave:
Thus, the crystallinity index (CI) was estimated at 0.67 degree of crystallinity indicating that roughly 35% of the α-cellulose in KT is in the amorphous region. The amorphous region was observed as open pores on the SEM micrograph in Figure 3 above. Structural variations in cellulose are thought to arise from the clarification by (Bolio-López, 2015) Bolio-López et al. (2015) about the entanglement of multiple cellulose chains through aggregation of hydrogen bonds to form cellulose fibrils in disordered regions (amorphous) or highly ordered (crystalline) in the extraction of cellulose fibers from Tó leaf petioles (calathea lutea) and characterization. XRD analysis of cellulose nanofibers and α-cellulose isolated from kenaf fibers and pomelo (citrus grandis) peel respectively by (Atiqah, 1813) and (Zain, 2015) in the extraction of cellulose nanofibers via eco-friendly supercritical carbon dioxide treatment followed by mild acid hydrolysis and the fabrication of cellulose nanopapers and preparation and characterization of cellulose and nanocellulose from pomelo (citrus grandis) albedo showed a crystallinity index of 92.8% and 57.47% which was explained to indicate a 7.2% and 42.53% presence of amorphous cellulose in the respective biopolymers.
Conclusion
The findings from this study show that α-cellulose recovered from kola nut testa possesses characteristics that can potentially turn its source from a worthless and scorned waste to a valuable raw material for the manufacture of a variety of products, ranging from food, pharmaceuticals and different household and industrial goods. It’s non-monetary value and excellent properties would compensate for the low yield of α-cellulose. The research has therefore opened a new frontier and widened the horizon in the search for alternative raw materials while providing yet another beneficial way to waste management and environmental sustainability.